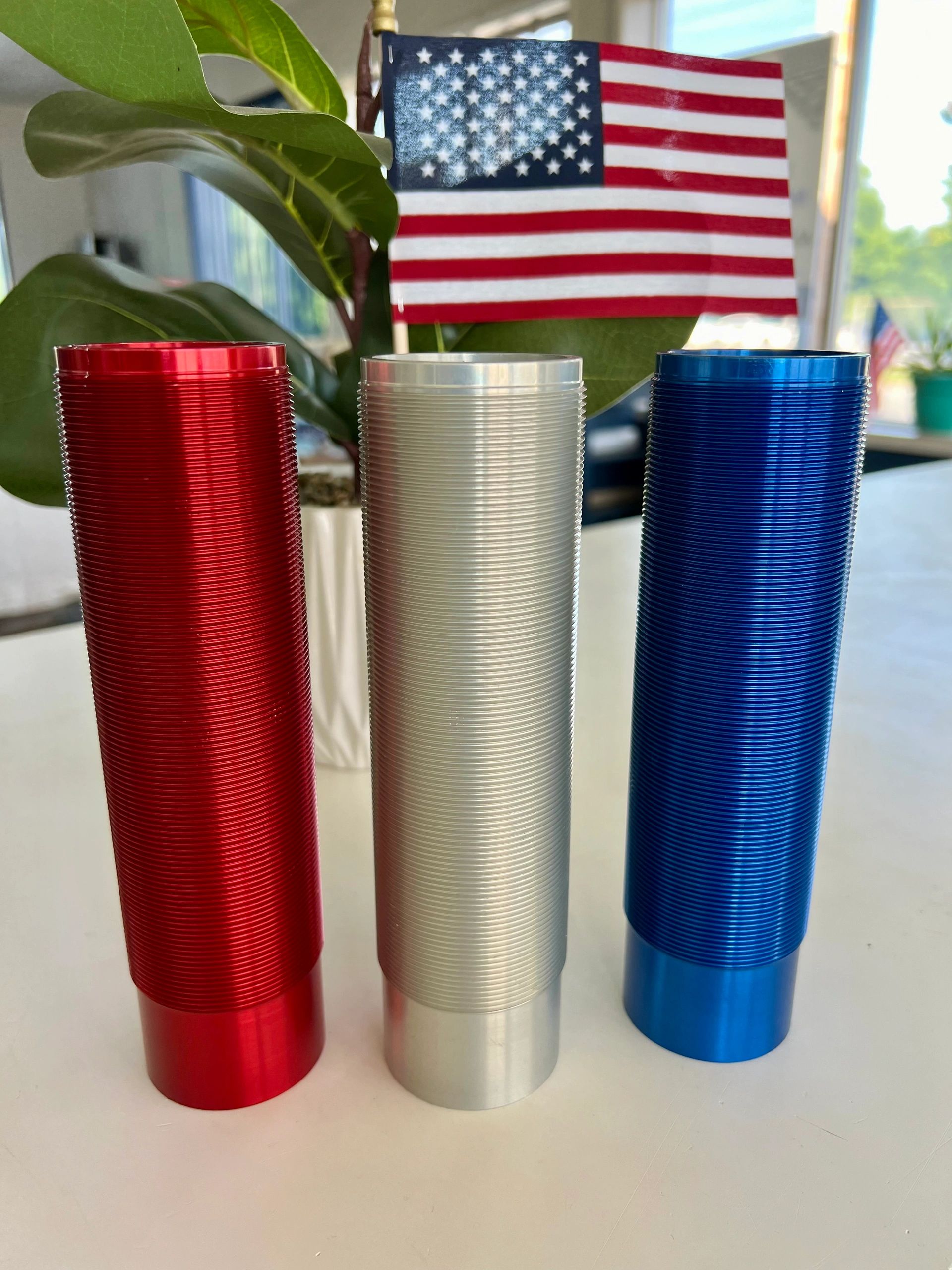
Our line is run by people, not an automated system which operate on an “assembly line” principle. Our staff follows your job from start to finish allowing them to take pride in their work and provide our customers with a high quality product & a level of service almost unknown in the industry. Our strict quality control measures will ensure that your parts will be consistent from one order to the next.
We use sulfuric anodizing—an anodizing process that uses a sulfuric acid bath—to achieve Type II & Type III anodized finishes. Anodizing is a controlled process which builds up the aluminum oxide on the surface of the material as well as into the aluminum material too! These finishes offer good corrosion and wear resistance and are available in vibrant colors.
Type II anodizing is the most common and most widely used form of anodizing.
The process is an electrochemical method that is performed by placing aluminum in a sulfuric bath and applying a prescribed amount of DC current to achieve the oxide thickness needed. The metal becomes an “anode” hence the name anodizing. This process builds up an aluminum oxide layer on the surface that also penetrates down into the aluminum material and forms an integral part of the metal. Typically, half of the coating thickness will be surface build up and the other half will be penetration into the metal. The resulting anodized surface is then ready to be colored or sealed.
The anodizing process stops the aluminum from corroding or turning white in the weather. Anodizing insulates the aluminum from electrical currents, making it useful as a commercial anodic finish for interior applications or light exterior applications that are cleaned often or exposed to outside elements. There is a clear anodize coating, but it is also can be dyed in multiple colors available on hand or a custom color. The different series of aluminum alloys play a big role in how the part will turn out!
One of the important benefits of Type II anodizing is its ability to offer corrosion and wear protection against environmental exposures. As a thinner finish (.0002-.001"), a Class II anodic coating is suited for interior applications or light exterior applications receiving regularly scheduled cleaning and maintenance. While Class II coatings offer good hardness, they are not as durable or wear resistant as Type III hard coating. It can however improve part aesthetics by allowing the part to be dyed in various colors. This is valuable in industries where aesthetic appeal is just as important as functionality. We offer:
Type II anodizing is an economical and affordable practice, especially when compared to the more expensive Type III anodizing.
Type III finishes provide improved wear, heat & corrosion resistance, improve surface for slide applications and they are non conductive. Hard Coat anodize thicknesses vary from 0.0005 to 0.006” (0.5-3 Mils) thick, depending on the specific aluminum alloy. In Type III anodizing half of the coating thickness penetrates into the surface of the parts while the other half builds up on the surface.
Although more expensive than type II, the benefits of Type III anodizing offers excellent corrosion resistance, similar to Type II, but with enhanced durability making it suitable for applications exposed to harsh environmental conditions, such as aerospace, fire arms and military components. Its superior abrasion and wear resistance ensures the longevity of parts where equipment is often exposed to extreme conditions.
Generates ultrasonic waves that create millions of tiny bubbles which gently cleans any surface they come in contact with. Excellent for removing oil from the parts.
Our cleaner is a high performance, non-caustic, non-silicated, alkaline cleaner, that is very effective in the removal of soils from aluminum surfaces. When used as directed, the cleaner will not etch the part surface.
After another 2 step rinse, the parts are dipped in an alkaline etch solution to remove surface oxides and metal from aluminum. The resulting surface is clean, smooth, and is ready for anodizing
After another 2 step rinse the parts are Rinsed in an acidic solution which removes unwanted surface alloy constituent particles not removed by the etching process.
After another 2 step rinse the parts are ready to be anodized. The anodizing takes place in an electrolytic solution, which is generally dilute sulphuric acid. A current is passed between the part (anode) and electrode (cathode). This causes oxygen to gather on the surface of the part, which reacts with the base metal to form a porous oxide layer
After another 2 step rinse we dip the parts in a 5% Nitric acid solution. The Nitric acid helps to further open the pores and flush out any aluminum sulphates.
After rinsing the newly formed anodic film is usually clear and very porous – it is very sensitive to absorbing color pigments. Many decorative colors, such as clear, red, blue, gold, and black can be attained by immersing the anodized parts in a dye solution.
We use a high quality sealant to prevent the color from leaching out and fading over time. It also helps the anodized part from absorbing impurities, such as fingerprints
This is the final step in our process. This further seals the part and helps the part dry faster when taken out of the tank.
Our rinse tanks operate with a filtration system with a continuous flow of deionized water! The water is continuously cycled through filters removing impurities as we move parts through the line. With this quality control measure in place, we aspire to make the best environment for your parts, as well as our tanks!
This high quality filtration system removes color, acids & impurities from our rinse water tanks to ensure clean parts before anodizing and to prevent drag out from tank to tank. This keeps our chemical tanks working at peak performance.
Our filtration system is monitored remotely by our vendor to ensure the best water and dependable operation for the anodizing process. With this system in place we can ensure our customers we have the taken the measures to provide the best outcome and quality to meet your expectations.
MINIMUM PRICING:
Type II minimum lot charge $125.00.
Type III (Hard Coat) minimum lot charge $170.00
Type II minimum price per part $0.55.
Type III (Hard Coat) minimum price per part Undyed $1.25 Dyed $1.35
Our Address is 245 South Oakland Avenue, Statesville, North Carolina 28677, United States
DISCLAIMER: Diversified Metal Finishing is not responsible for surface defects or damage during Type II or Type III anodizing if no alloy is specified on an engineering print. Submitting parts without alloy specs implies acceptance of these risk
Mon | 08:00 am – 04:30 pm | |
Tue | 08:00 am – 04:30 pm | |
Wed | 08:00 am – 04:30 pm | |
Thu | 08:00 am – 04:30 pm | |
Fri | 08:00 am – 04:30 pm | |
Sat | Closed | |
Sun | Closed |
We are closed on major holidays.
Quick turn around times and high quality is what we strive for! Call us for more information!
We use cookies to analyze website traffic and optimize your website experience. By accepting our use of cookies, your data will be aggregated with all other user data.